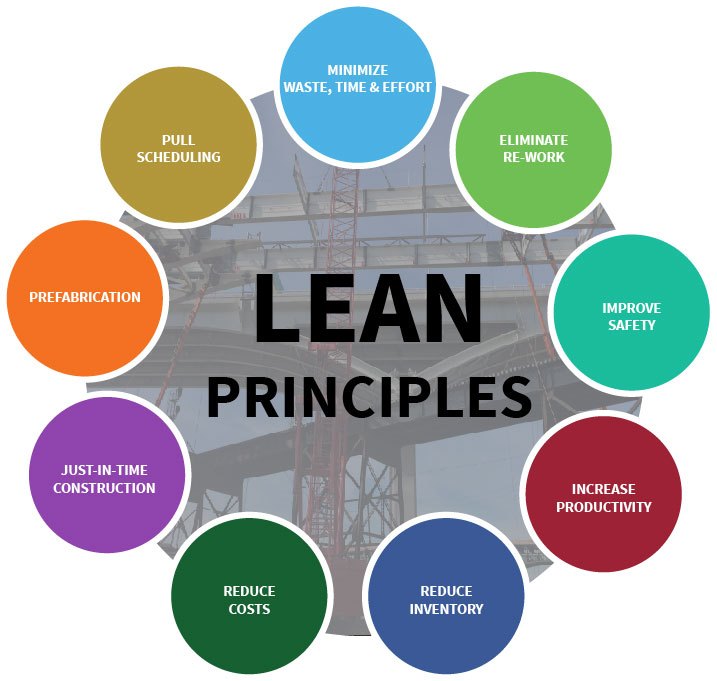
Using as few resources and generating as little waste as possible is at the heart of the Lean philosophy. Continuous experimentation and zero waste are the hallmarks of lean manufacturing. Together, lean thinking and practice are essential to its success.
A Lean practice begins with the work that creates value for the customer and the people who do the work. Workers and managers can improve the quality and efficiency of their work and the amount of time and effort it takes by constantly experimenting and trying new things. As a result, lean organizations can better adapt to their ever-changing environment than their peers because of the systematic and continuous learning engendered by lean practice.
Through product and process development, through fulfillment from the order through production to delivery, and through the product's and service's use cycle, a lean enterprise is organized to keep understanding the customer and their context, i.e., specifying a value and looking for better ways to provide it:
• Whether it is an established company or a startup, a lean enterprise is constantly reassessing its purpose, process, and people.
• Is there a reason why this is important? Alternatively, what's the issue?
• What needs to be done to fix the problem?
• What skills and abilities are needed to solve this problem?
• What operating system and leadership behaviors are needed to implement the management system?
• As a purpose-driven socio-technical system, what basic thinking, including mindsets and assumptions, are necessary for the organization to function?
A moral compass guides lean practitioners' work: they believe that treating people with respect and fairness will lead to better outcomes for everyone involved. Lean isn't a religion. It's not a set of beliefs and methods that are fixed and unchanging. Instead, it progresses in the context of a specific set of circumstances. There is no end in sight as long as the value is created imperfectly and waste is present. Learn about lean thinking and practice's short history.
Let's step things up. It's worth celebrating. The work should be treated with the utmost respect as well.
Lean's 'Muda' wastes, or 'Muda.'
In Lean, the seven wastes are considered the root of all unprofitable activity in an organization.
"Something that does not add value" is the simplest way to describe waste in the context of Lean methodology. You cannot expect customers to pay for anything that does not add value to their needs.
The seven wastes are:
Several things can go wrong with a product
The most obvious of all seven wastes; defects are also the most difficult to spot before they reach your customers. The cost of any mistakes made in the manufacturing process or the quality of the products themselves is enormous.
There is a lot of overproduction
Your company's problems can be hidden by high levels of inventory caused by overproduction. Batch processing, creating more supply than demand, etc., are two of the most dangerous forms of overproduction in lean methodology.
Transportation
A wasteful practice moves materials from one place to another without adding any value to the final product.
Waiting
In our professional lives, we spend a lot of time waiting for things to happen. One of the most dangerous and pervasive wastes is waiting for an engineer or member of the team, often through more bureaucratic processes that can take a long time to remedy or minimize.
Keeping track of all of your belongings
You have to pay for every piece of product in inventory, whether it's raw materials, work-in-progress, or finished goods.
The motion of the body
Wasted motion can be defined as any unnecessary movement, such as a machine that requires more effort than necessary to operate or workstations that are far apart and require movement between.
Processing
Using small and appropriate machines where they are needed in the flow is far more beneficial than using massive machinery that can halt the entire process for days on end in lean.
#lean
#stoepplantjes
#experiment
#value
Here are your recommended items...
Here are your milestones...
Choose a gift to support your favorite creator.
Send appreciation in cash choosing your own custom amount to support the creator.
CustomFeature the author on the homepage for a minimum of 1 day.
$15Send a power-up (Heart Magnet, View Magnet, etc.).
Starting from €2Boost the user's post to reach a custom amount of views guaranteed.
Starting from €5Gift a subscription of any plan to the user.
Starting from €5Send cheers to Bhargav with a custom tip and make their day
More hearts on posts (24 hours)
€22x Stars for 1 hour
€2Reward the user for their content creation by encouraging to make more posts. They receive extra rewards per heart.
€5More views on posts (48 hours)
€10Level up with one level
€10The campaign will be active until the end date, but your selected goals will be achieved within the delivery timeframe you selected.
Standard duration is 5 days, but you can extend it up to 30 days.
An error has occured. Please contact the Yoors Team.
An error has occurred. Please try again later